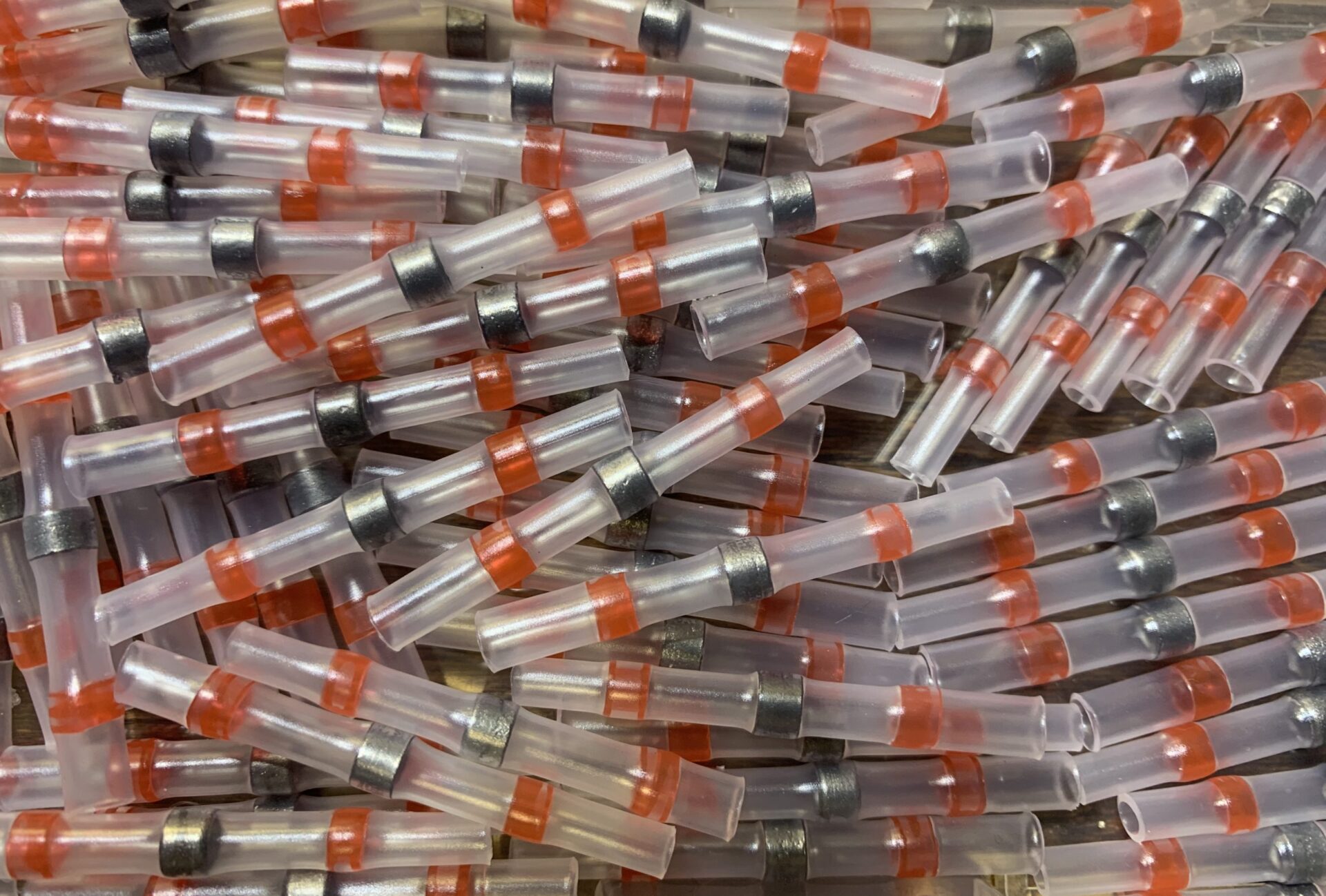
Solder-Seal Connectors
Important Notice
This site is no-longer being maintained, and the content and links found here may be irrelevant and outdated. It is online for archival purposes only.
Doing pixels- I use these red ones the most. The white ones are excellent for smaller wires like data cables.
These things are a godsend to anyone who tinkers with electronics or repairs low-voltage systems in cars, boats, etc. I can’t imagine working with pixels without them. Sure- you can solder connections and shrink tube them, but when you have to do dozens or hundreds- it’s very tedious and slow. These things make it EASY!
You can find them on Amazon.com, ebay.com, and aliexpress.com, among others. I’m not sharing direct links just because they can expire and I don’t currently do affiliate links. Just search for “solder seal connectors”, or “heat shrink solder connectors” and you will find lots of them. I suspect they are all made by the same factory in China, so I don’t have any kind of brand loyalty. Most that I buy on eBay and direct from China are “unbranded”.
These are NOT the same as heat shrink crimp connectors. I hate those things (I generally hate ALL crimp connectors, except for the ferrules for stranded wire). I don’t trust the heat shrink crimp connectors because the crimper can damage the heat shrink insulation.
I’ve seen a lot of love/hate for these things in online forums. I suspect a lot of the haters just haven’t worked with them very long and have made mistakes, or don’t have the right tools. I’ve used them hundreds (close to a thousand at this point) of times and they are my go-to for connecting low voltage wires together now.
I want to share how I work with them, very successfully…
First- you need the right tool- a good heat gun, preferably with a smaller nozzle or a “concentrator” nozzle. You want something that puts out a lot of heat fast. You can’t think of these things like old-school shrink tubing- they take high heat and work fast.
Not advertiing this brand, just what I use. Smaller nozzle works better.
Contrary to what you may see in online video ads- using a match, lighter, soldering iron, butane torch, or really anything else won’t work well. I have used a small butane torch in a “heat gun” configuration in a pinch, but you need to be very-very careful with how you use it in order to be successful. (Hint: keep it moving, never hold it in one place. You want to heat the whole connector- not just the solder ring.)
Steps for success:
- Use the smallest solder-seal connector you can stuff your wires with insulation into. Ignore the “AWG” ratings- different insulation will make the wires fit in differently. You definitely don’t want things too loose, although these can shrink a LOT. If you can get a fairly tight fit- it’s easier to work with too as the wires are less likely to slip out while you are connecting them.
If you are connecting slightly different sizes of wires, or are bundling multiple wires into one connector, take note that one side of the connector is slightly larger than the other. You can use this to your advantage! - You only need to strip about 1/4 of an inch of insulation, although if you are working with the big blue or yellow ones- you can go up to about 1/2″. Don’t strip too much- you want your insulation well inside the colored heat shrink seals inside the ends of the tubes.
- You don’t have to twist the wires together. This is tedious and just adds frustration. You are soldering- and the shrink sleeve will provide additional mechanical support. You DO need to make sure your bare conductors overlap each other inside the solder ring. Don’t expect the solder to bridge any kind of gap.
Use care with heavier stranded wire- be sure the conductors are straight, and there isn’t one sticking up perpendicular to the connector. These can actually puncture the connector when heating, which can create a point for an electrical short, or for solder to leak out. - I like to pre-heat the gun, although newer guns heat up very fast (within seconds). Again- you want a smaller nozzle. Ideally, the nozzle should be no wider than the length of the connector, and I prefer a bit smaller. The reason for this is it is very easy to burn/melt the insulation on your wires before you solder-seal connector has done its thing.
- Hold the connector about 3/4″ above the nozzle. If you don’t have a small nozzle/concentrator- it may be best to hold it off to the side a bit so the heat isn’t blowing directly on your insulated wires. The insulation on your wires will generally melt/burn faster than the solder-seal will.
I’ve been successful heating 2-3 seals at a time, as long as they are right next to each other. This can save you a lot of time, especially working with LED pixels which generally require 3 connections. - Watch the connector carefully while holding it as steady as possible by the wired on either side. Obviously don’t get your fingers very close to the heat gun nozzle- you would be amazed at how fast you can get burnt.
The seals on either side will melt quickly, and you can pretty much ignore them. You are watching the solder ring. As soon as you see it melt/collapse- remove it from the heat. DO NOT heat any longer. Think like microwave popcorn- there is a narrow range of time between good and burnt! The second that solder melts- your connection is complete. - Now- gently set your new connection aside for at least 30 seconds. DO NOT pull on the wires and try to avoid flexing them. If you pull on the wires before the solder and plastic set- you will stretch it and pull your wires out or break your connection. I’ve seen videos that show people immediately pulling on them after heating- just don’t!
- If you can pinch the solder portion of the connector in your fingers and it doesn’t burn (it can still be warm, but not HOT), then you can work with it. Generally if you follow the instructions above- this should only take about 30 seconds.
- That’s it. Easy! If anything- practice on some scrap wire to get the hang of it before you work on your actual project. Remember- if you screw up you will have to cut and strip your wires again- you don’t want to have to do that too many times, and may not even have the extra wire slack to do it for your project.
Note that in my instructions above- I am using the heat gun on my workbench as pictured, and am bringing the connector to it. I’ve found this is the easiest way of working with these connectors while avoiding any collateral damage. It is very easy to control the heat and insure that nothing else is in contact with it.
You can, of course, and may even need to bring the heat gun to your connector. This is obviously necessary “in the field”, but may also be required when working on larger projects that you simply can’t move. If this is the case:
- You need to be very careful when aiming a heat gun- look well past and all-around your target, in this case, the connector.
I’ll be honest- I actually scorched a section of carpet in a room I was working on some Pixel props in because I wasn’t being careful. I’ve also burned myself more than I care to admit, and have had plastic pipes, LED holder strips, and coro melt. Heat guns can melt, scorch or burn just about anything! Take them seriously- they aren’t just glorified hair dryers. - The other rules apply- keep the heat gun centered on your connector and watch the solder ring very carefully. Remove the heat the second you see it collapse/melt. Since you are removing the heat by moving the heat gun- be careful where you aim it while turning it off!
Problems that can occur:
If the solder squirts out of one of the ends of the tube:
- There may have been a conductor strand that got folded back and was sticking out. Solder follows the conductors- so it will follow it out.
- You may be using a connector that is too big for your wires. If it can’t shink enough and seal, the solder will find its way out.
- It may have been overheated or heated too fast, and the seal wasn’t melted enough or strong enough to keep it inside. You may need to actually move your connector a bit further away from the heat gun. This gives you slightly more working time but helps give the seal time to melt before the solder.
(Solder) Blow out:
- This is almost always the result of heating for too long or not using the right tool.
- If you have to use a small butane heat gun, for example, it’s important to keep it moving up and down the length of the connector to try to heat it evenly. It concentrates a large amount of heat in a tiny area and can quickly burn the heat-shrink material.
- If you are using an electric heat gun (recommended), remember again- remove the connector from the heat immediately when you see the solder ring melt. Continuing to heat can melt/burn the connector.
Solder not melted and connector scorched:
- You are either using an unsuitable heat source (like an open flame) or are using something that isn’t generating even heat that is high enough to properly shrink the connector and melt the solder.
- Not enough heat can actually do this- the heat shrink plastic of the connector can melt and start to burn before the solder gets hot enough to melt.
- Again- use a quality heat gun with these connectors! Save the lighter or butane torch for “emergency” repairs.
Wire insulation melting/burning:
- This can happen because the connector is made for higher heat than most connecting wire insulation is. You can prevent it by using a nozzle slightly smaller than the connector itself, and again- time things carefully.
- Don’t worry about the very end of the connector. if it doesn’t shrink completely, it’s still just fine as long as the seal area itself melts. If you take extra time to make sure the ends are shrunk completely- you may end up applying too much heat. You will see in my picture below that the red connectors flare out a little bit at the ends- this is just fine. Heating them longer is just an “appearance” thing, and can ruin the connector or wires.
- It isn’t the end of the world if the conductor isn’t exposed- it just doesn’t look good and may reduce the lifespan of the wire insulation.
- If the conductor is exposed- you can use some liquid electrical tape on it or even actual electrical tape. If the other end of the wire is loose- you can also just cover it with conventional shrink tubing. Ideally though- you should cut off the connector and do another one.
- It is possible that the wire you are using has really poor insulation that can be easily melted. If it is a recurring problem and you have followed all of the other advice above- you might consider a different supplier. Wire with insulation that is VERY prone to melting is really unsafe for electrical use anyway.
Here is a typical example of the connections I routinely do. The splices can flex a bit on their own as they heat/cool, but it is important that you NOT force them to flex or pull on them while they cool.
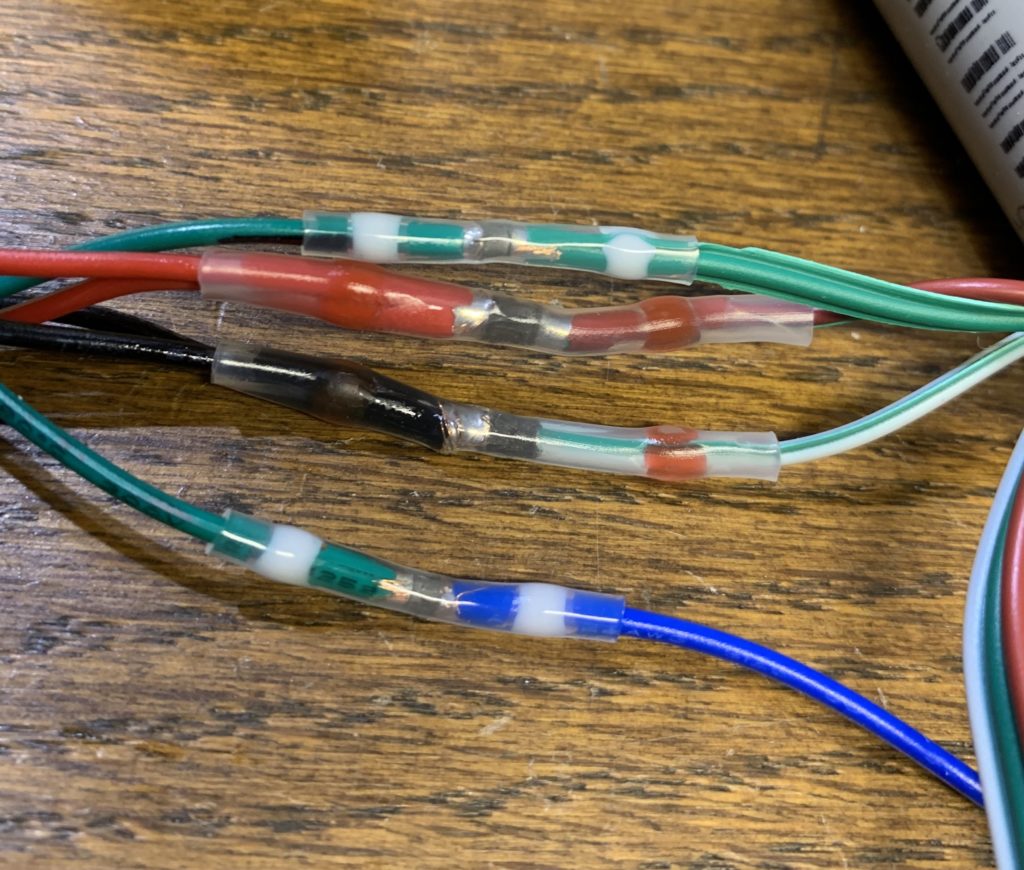
These generally don’t have any kind of “ratings” as far as electrical specifications, so I recommend sticking to low voltage applications. I have used them for some LOW CURRENT AC work, but recommend Wago connectors or old-fashioned wire nuts for higher currents/voltages.
Also- if you plan to bundle them together or cover them with additional heat-shrink- be sure to inspect them carefully for any holes, wire poke-thrus, or solder leaks to prevent the possibility of shorts. If done right- they are well insulated and completely safe.
Hopefully this helps some of you when working with these connectors. They can save you hours or even days of work if you do LED pixels. I also use them for my 3D printer’s splices, and for connecting other controllers and devices together.